PROVA DI DUREZZA ROCKWELL (HRC)
Il metodo di
durezza Rockwell consiste nel misurare la differenza di profondità dell’impronta lasciata da due diversi carichi nominati precarico o carico iniziale, e carico maggiore.
Per contro, la
tecnica Brinell, come oure Vickers e Knoop, si affida alla valutazione ottica delle dimensioni dell'impronta creata dal penetratore.
Nella tecnica Rockwell, i carichi vengono applicati con diversi valori di forza ciascuno e le loro combinazioni generano diverse scale di misura. Fissata la scala, i valori che appartengono ad essa, ottenuti durante la misura di durezza, possono essere confrontati tra loro.
Normativa Durezza Rockwell
Il processo di misurazione, rigorosamente definito dalla norma ISO 6508, si basa su principi ben consolidati che garantiscono la ripetibilità e l'affidabilità dei risultati attraverso l'uso di specifiche procedure e apparecchiature.
I parametri chiave di questo processo, come la forza di carico applicata, il tempo di mantenimento della pressione e la profondità di indentazione, sono essenziali per garantire che la valutazione sia conforme agli standard internazionali.
La norma ISO 6508 copre dettagliatamente queste specifiche, stabilendo un quadro preciso per l'esecuzione della prova, che include la selezione del corretto penetratore e del carico di prova in funzione delle caratteristiche del materiale esaminato.
Questo approccio metodico permette di determinare con precisione il valore di durezza Rockwell, fornendo un indicatore affidabile delle proprietà meccaniche del materiale, quali la resistenza all'usura e la capacità di sopportare sollecitazioni senza deformarsi permanentemente.
Esecuzione della prova Rockwell
Come indicato nello schema di Fig. 1, la grandezza che viene misurata nella prova Rockwell è la profondità di penetrazione h (affondamento del penetratore) ottenuta dalla differenza tra la profondità totale fino a fine prova, che consta del contributo dato dal precarico F0 e dal carico maggiore F1, e la profondità data dal solo precarico.
La norma ISO 6508 specifica le scale di durezza Rockwell da utilizzare in base al penetratore scelto e al carico applicato, fornendo una guida chiara per la selezione della combinazione più appropriata per ciascun materiale. Questa selezione accurata assicura che la misurazione della durezza sia non solo precisa ma anche direttamente comparabile con altri test eseguiti sotto condizioni standardizzate.
Per materiali dolci viene usato come tipologia di penetratore una sfera che può essere di acciaio temprato o di metallo duro, con la desinenza S o W rispettivamente (scale HRBS e HRBW, scala HRTS e HRTW).
Per materiali molto duri si usa invece un penetratore, detto indentatore di Brale, costituito da un cono di diamante con un angolo al vertice pari a 120° (scale HRC o HRN). I carichi variano tra F=60Kg e F=150 Kg.
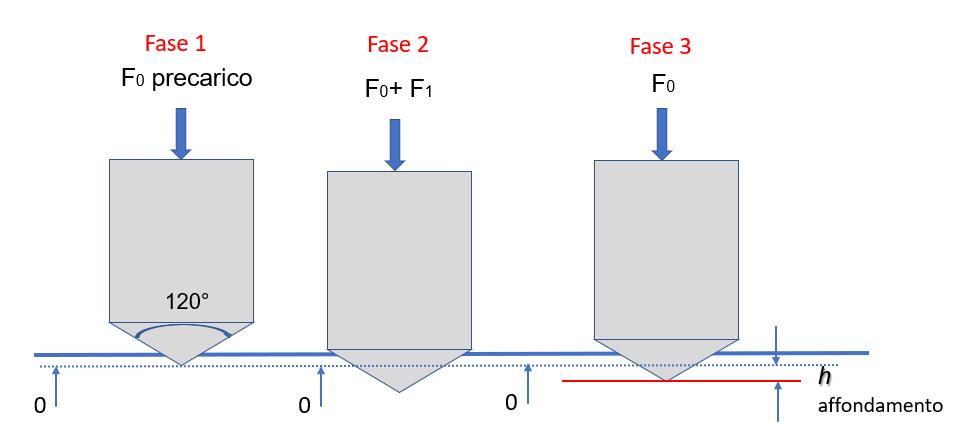
Preparazione del campione
La preparazione del campione e la scelta del penetratore sono passaggi fondamentali nel processo di misurazione della durezza Rockwell, determinanti per l'accuratezza e l'affidabilità dei risultati ottenuti secondo normativa.
Prima di procedere con la prova di durezza, il campione deve essere preparato con attenzione, assicurandosi che la superficie di test sia liscia e pulita, libera da qualsiasi contaminazione, ruggine, olio o altri residui che potrebbero influenzare l'impressione del penetratore. Questa attenzione preliminare è cruciale, poiché irregolarità superficiali o preparazioni inadeguate possono portare a misurazioni imprecise o fuorvianti della durezza.
La prova consta dei seguenti passaggi:
- Sulla superficie del campione oggetto di misura viene applicato un predeterminato precarico F0 che produce una impronta la cui profondità viene utilizzata come “taratura” per la misura successiva.La durata d’applicazione del precarico non supera i 3 s.
- La fase immediatamente successiva prevede l’applicazione del carico maggiore F1 per un tempo t dopo il quale viene rimosso e il sistema ritorna alla sola condizione di precarico. Viene quindi misurato l’affondamento h.
Misurazione e risultati.
Il valore oggetto di misura per la determinazione della durezza Rockwell HR, come già specificato precedentemente, è quella dell’affondamento h, espresso in mm. In particolare il valore della durezza Rockwell si ottiene sottraendo il valore di h ad un numero convenzionale N e dividendo poi per un fattore S, dipendente dal carico maggiore F1, applicato dopo aver azzerato lo strumento con un precarico F0 definito (98,07 N per tutte le scale A÷K e 29,42 N per le scale N e T), secondo la formula per la durezza Rockwell in Fig. 2.
N vale 100 per le scale A, C, D, N e T, mentre vale 130 per le scale B, E, F, G, H e K; S vale 0,002 per le scale A÷K, mentre vale 0,001 per le N e T.
Nella pratica, viene letto sul durometro, il valore di durezza Rockwell sulla scala ottica o sull’indice dello strumento, o in forma digitale.
Il valore della durezza Rockwell è rappresentato da un numero adimensionale, seguito dal simbolo HR e dal codice alfabetico od alfanumerico della scala usata. Le scale di durezza HR normate sono 15, ma le più usate sono: HRC, HRB. In caso venga usata la scala B, è inoltre necessario indicare il materiale della sfera aggiungendo la lettera S (sfera d’acciaio) o W (sfera di metallo duro).
Vantaggi della prova di durezza Rockwell
La prova di durezza Rockwell (HR) offre i seguenti vantaggi:
- Metodo di misura della durezza rapido;
- La misura può essere automatizzata e non necessità dell’utilizzo della microscopia, quindi efficiente e meno costoso;
- Minore criticità nella preparazione della superficie rispetto al metodo Brinell e Vickers;
- A differenza della durezza misurata col metodo Brinell e col metodo Vickers, la durezza Rockwell tiene conto del recupero elastico del materiale, grazie all’utilizzo del precarico come “taratura” e successiva misura.
Svantaggi della prova di durezza Rockwell
Gli svantaggi del metodo di prova Rockwell possono essere brevemente riassunti:
- I valori della durezza ottenuti col metodo Rockwell si basano su un calcolo (formula) diversa rispetto ai metodi Brinell e Vickers, utilizzando numeri convenzionali pertanto le correlazioni con altri valori di durezza e proprietà di carico a rottura del materiale non sono attendibili;
- Un piccolo errore nella misura dell’affondamento viene amplificato quando viene calcolato il valore della durezza;
- La prova e quindi il valore della durezza è influenzato dalle condizioni di prova ossia dalla eventuale presenza di contaminazioni, ossidi, tracce di lubrificante e dallo stato di usura del penetratore.